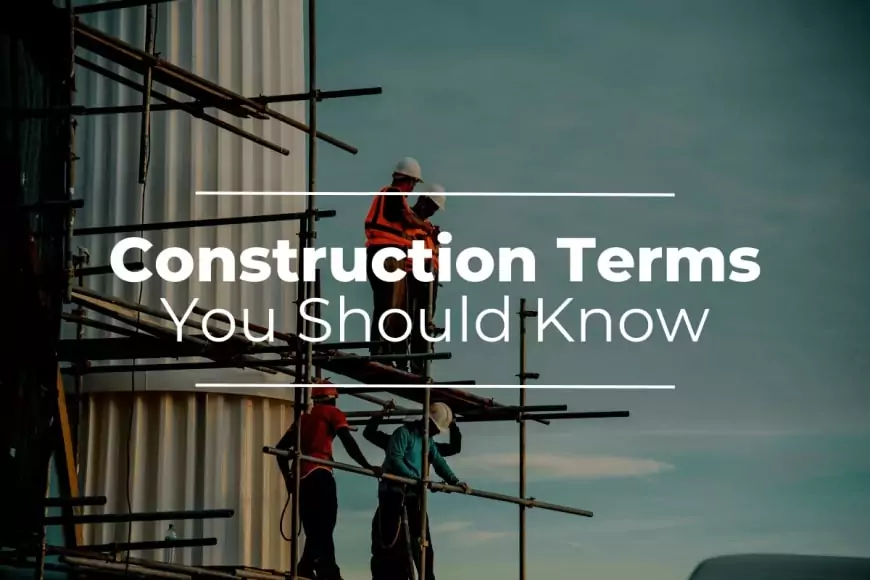
Construction is a complicated beast that sometimes uses a language of its own. Whether you’re a seasoned construction professional or simply interested in learning more about the field, having a solid understanding of daily jargon is essential. In this blog, we’ve compiled a list of 100 construction terms that you should know. This list covers the most common terms used in the construction industry, from foundation to finishing touches. So, whether you’re a builder, operator, foreman, or business owner, read on to expand your construction vocabulary and deepen your understanding of this fascinating field.
- Aggregate: A particulate material that is made up of sand or crushed stone. Aggregates are used in materials such as concrete and are a fundamental part of building foundations.
- All-In Rate: Total project expenses including all direct and indirect costs.
- Backfill: Refilling excavated areas with soil or other materials to restore the original grade or elevation.
- Beam: Beams run horizontally along the main walls of a building at ceiling level, supporting the structure.
- Best Value Method: A construction procurement method where contractors are awarded the bid based on prices and quality measurements from previous work performance.
- Bid: A formal proposal submitted by a contractor or subcontractor to perform work for a specific project.
- Bid-Hit Ratio: Ratio involving where you have successfully bid on a construction project.
- Bid Selection: The process of examining and comparing contractors’ bids to select the right one based on price and services provided.
- BIM (Building Information Modeling): A 3-D modeling process that features the details of the building.
- Blocking: A construction technique to join, fill or reinforce the building structure.
- Blueprint: A detailed architectural or engineering plan showing a building or structure’s dimensions, materials, and placement of elements.
- BOQ (Bill of Quantities): An itemized contract document featuring all the materials and workmanship used to help price out the project.
- Building code: A set of regulations establishing the minimum standards for building design, construction, and safety.
- CAD (computer-aided design): Architecture software used to create detailed building models.
- Cant: An angled surface or line that cuts a corner off.
- Caulking: A flexible, rubbery material type used to seal gaps in a joint.
- Ceiling joist: Parallel framing members that support ceiling loads and are themselves supported by load-bearing walls.
- Change Order: A written order that changes the original scope of work, schedule, or price of a project.
- Circuit breaker: A switch in the electrical panel that shuts off power to certain parts of the building.
- Closeout: The final stage of a construction project where all documents, warranties, and final payments are completed and the project is turned over to the owner.
- Concrete: A building material created by a hardened mixture of cement, gravel, sand, and water. It is used for slabs, columns, and other types of structures.
- Concrete Slab: A horizontal platform used to construct the ceiling or the floor of the building.
- Construction Management Software: An application used by construction managers to efficiently run the project as it features accounting, documentation, and team workloads.
- Cost Codes: Codes used to track budgets and expenses of labor activities.
- Course: Concrete blocks, stones, or bricks in a continuous masonry row.
- Cross Bracing: Reinforcements in an X-shape that enhance a structure’s durability.
- Cut and Fill: The process of leveling and balancing a construction site by removing soil (cut) from higher areas and adding it to lower areas (fill).
- Daily Report: A report that documents materials installed, crew information, safety incidents, and work completed as the document is created by the foreman at the end of each day.
- Damp Proofing: A procedure used to keep the drywall interior dry and to prevent moisture absorption.
- Diagrid: Structure reinforcement technique using steel beams placed in diagonal grids.
- Dimension: A dimension is used in the planning stage and refers to a measure between two points.
- Drywall: A panel made from gypsum plaster wrapped in cardboard. It is commonly used as a fundamental material for framing a building.
- Ducts: Piping that carries air throughout a structure.
- Egress: A way of exiting a structure, such as a window or a door. Laws require a certain number of egress windows in certain parts of a home.
- Elevation Drawing: A drawing of a structure that shows the front or side of the facades of the buildings; it is a first-angle projection.
- Encasement: The encasing of underground pipes in concrete or when encasing hazardous materials that have been installed.
- Falsework: A temporary structure used to support an arch or bridge during the construction or repair process.
- Field Measure: Measurements taken inside the structure that does not rely on blueprints.
- Field Work Order: The general contractor’s document given to the subcontractor regarding the completion of work that is not included in the project’s original scope.
- Floor Plan: Drawing of the building’s layout providing details of each room space from an overhead view.
- Foreman: The leading supervisor at the construction site who is in charge of the work crews. He ensures workers perform daily tasks based on established schedules while creating documents regarding completed work.
- Formwork: Temporary molds or structures used to support concrete or other materials while they set or harden.
- General Contractor: The main contractor for the building construction. Their main responsibility is the oversight of the project as they manage subcontractors, handle scheduling and monitor the budget.
- Girder: The main horizontal support of a structure that supports smaller beams.
- GMP (Guaranteed Maximum Price): A contract where the contractor is paid for the actual costs that are incurred in addition to a fixed fee that has a price ceiling cap.
- HVAC: An abbreviation for heat, ventilation, and air conditioning.
- I-beam: A beam with a cross-section that looks like the capital letter I. Girders often have an I-beam cross-section.
- IFB (Invitation for Bid): Request given to contractors for them to submit a project proposal regarding their provided services and products.
- Insulation: Material that’s designed to prevent heat from leaving or entering a building. Insulation material is placed within a structure’s walls, ceiling, or floor.
- Job Costing: The calculation of the total cost of a project, including labor, materials, and overhead expenses, to determine profitability and ensure accurate billing.
- Joint: A construction interface between two separate building elements that do not have a physical connection to each other but may overlap or align to the other element.
- Joist: The location where the surfaces of two components are joined.
- King stud: A framing member that runs from the bottom to the top of a panel or sheet.
- Lath: A metal wire on the frame of a building that serves as a base for laying down stucco or plaster.
- Lien: A property claim made by the contractor against the owner when they are not paid for the completed work.
- Lift Slab Construction: Construction method where concrete slabs are cast on the ground level and then are lifted into place using hydraulic jacks.
- Load-bearing wall (partition): A partition or load-bearing wall carries the load of the structure above it. As a result, they cannot be removed without compromising the structure’s integrity.
- Lump Sum Contracts: A contract where a single price is quoted for the entire construction project.
- MEP: An abbreviation that stands for Mechanical, Electrical, and Plumbing. They are the technical aspects that make a building habitable.
- Moling: A pneumatically-driven device inserted into the ground to create holes for construction elements such as pipes and heat pump systems.
- Mortar: In masonry, mortar is the paste that is used to bind stones, bricks, and other similar types of units used to construct the walls of a building. Mortar can be made up of a variety of things, such as asphalt, pitch, or clay.
- Particle board: A substitute for plywood that is composed of sawdust mixed with resin.
- Plywood: A panel of wood that is made from multiple layers of veneer, compressed together.
- Precast Concrete: Concrete elements created offsite that are transported to the construction site for final assembly.
- Prefabrication: A construction method that involves manufacturing building components or entire structures off-site in a factory or other controlled environment.
- Prevailing Wage: The minimum hourly wage, benefits, and working conditions required by law to be paid to workers on public construction projects.
- Project Manager: The project manager handles the entire management of the construction project. They oversee project deliverables, schedules, and budgets.
- Punch List: A list of unfinished or defective items that need to be completed or fixed before a project can be considered complete.
- Punch-out: The final inspection and correction of any outstanding items or deficiencies prior to project completion.
- Purchase Orders (PO): In construction, a purchase order is a document from the buyer that indicates their intent to purchase services and products from the seller, such as a supplier.
- Purlin: A horizontal and longitudinal beam used on the roof structure to support the rafters.
- PVC: Short for polyvinyl chloride, this common plastic is used most commonly for water pipes and sometimes for flooring.
- Rafter: A series of roof frame pieces that are connected to the supports and hold up the roofing and sheathing.
- Retainage: A portion of the contract price is withheld by the owner or general contractor until the project is completed to ensure the contractor’s performance.
- RFI (Request for Information): This preliminary document contains general information about the capabilities provided by potential vendors or suppliers.
- RFP (Request for Proposal): A document request to vendors to obtain an overview of their costs and offerings for specific services.
- RFQ (Request for Quote): A document featuring predetermined specifications for the project as it requests the vendor’s costs to fulfill these specifications.
- Rim Joist: In flooring, a rim joist is attached to the end of the main joists to give lateral support.
- Rough-In: This is the stage in construction where the mechanical, electrical, and plumbing lines are brought into the project. During the rough-in, the basic framing of the project is complete, but the final connections of the project are not complete.
- RTT (Request for Tender): A formal invitation to vendors to submit their bid to supply products and services to the construction project.
- Rubblization: During the construction project, unwanted concrete is broken down into small pieces that are used in the base for new surfaces.
- Schedule of Values: A project’s work item list that corresponds the items to their value as the list represents the entire amount of the work project.
- Scope of Work (SOW): A detail in the agreement outlining the work that will be performed for the project.
- Section Drawing: A drawing that shows the building’s view as if cut on a vertical plane.
- Shoring: A construction method that uses wood or metal props to support the structure while it is worked on.
- Skirting: Material that covers up the joint between the floor and a wall in the interior of a building, for aesthetic purposes.
- Stucco: A material made from aggregates, a binder, and water. It is often used as a decorative coating on walls and ceilings.
- Subcontractor: The subcontractor is specialized in a specific construction or building trade, such as electrical or plumbing. They are contract workers who the general contractor hires.
- Submittal: A formal process of submitting shop drawings, product data, and samples to the design team for approval prior to installation.
- Superstructure: A structure that is built on top of another structure.
- Takeoff: A document that lists the types and quantities of materials that will be required for the construction project.
- Tender: A contractor’s or supplier’s submission response about the supplies and services that they can offer to the project when receiving a bid invitation.
- Time Tracking: The process of monitoring and recording employee work hours for payroll and project management purposes.
- Toolbox Talks: Short safety meetings conducted on a regular basis to discuss job-specific hazards, safe work practices, and other relevant topics.
- Trim: The materials used to provide a clean finish of the building, such as moldings around window and door openings, or the baseboards in rooms, for example.
- Underpinning: Construction technique to strengthen the foundation of an existing structure with the use of beams, concrete or base pining.
- Value Engineering: A process of optimizing the value of a project by reducing costs while maintaining or improving functionality and quality.
- Veneer: A very thin sheet of wood. It is typically a finer wood that is used as a decorative cover for lower-quality wood.
- Warping: A distortion of material, which can be a sign of water damage.
- Zoning: Government regulations that dictate how property areas can be used.
In conclusion, the world of construction is vast and complex, and mastering its specialized terminology is essential for anyone working in the field. We hope this list of 100 construction terms has been helpful in expanding your knowledge and vocabulary. Whether you’re involved in building projects or simply interested in learning more about construction, these terms will help you communicate more effectively and understand the industry’s nuances. With these terms in your tool belt, you’ll be better equipped to navigate the world of construction and make informed decisions about your projects.