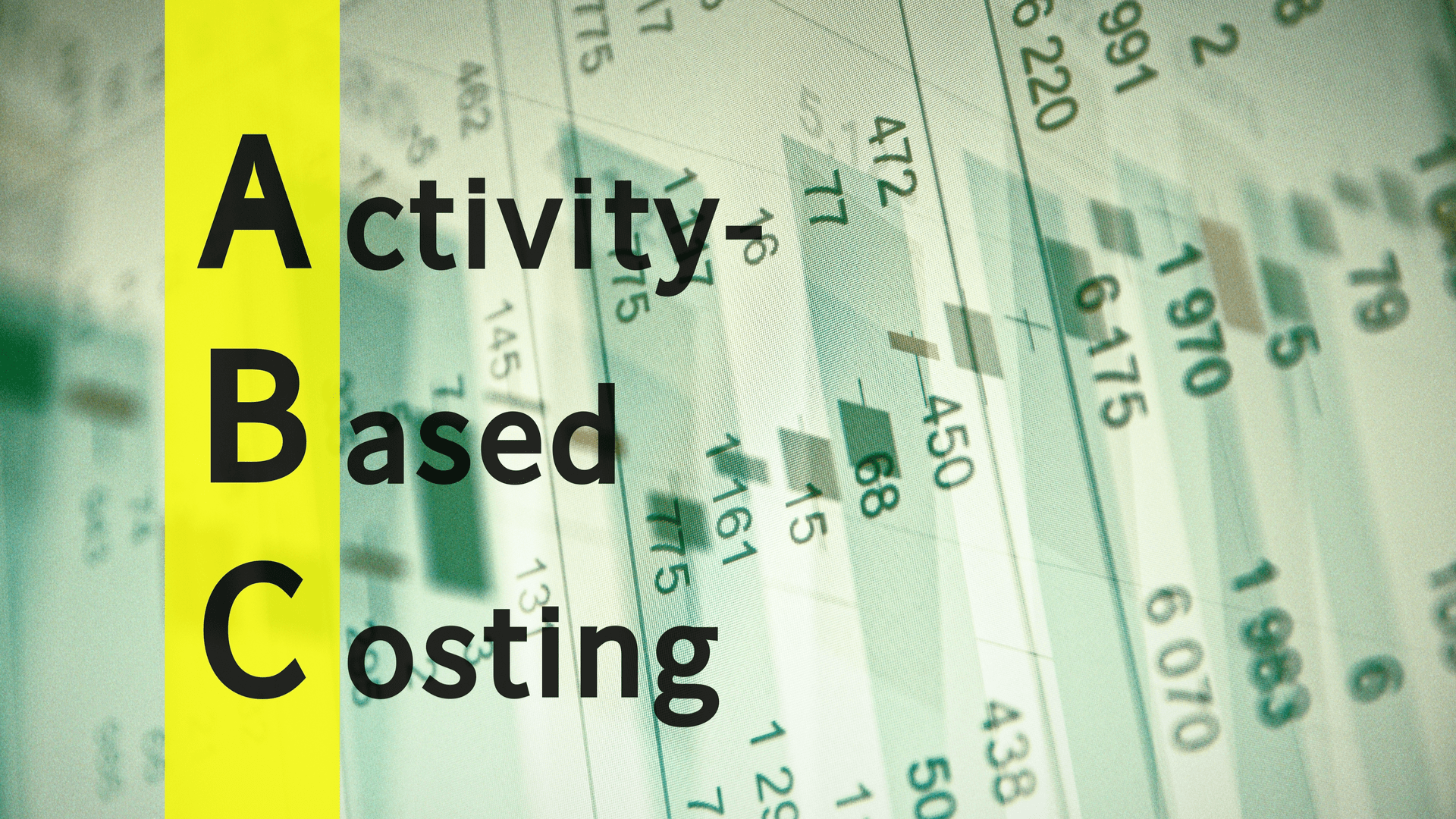
Accurate Job Costing is Key to Profitable Pricing
When your crew gets together in the shop before starting a day’s work, there’s a lot of money being spent before they finish their first cup of coffee. Even though they haven’t clocked in on a job yet, your business expenses are already adding up.
It Takes Money to Make Money
The cost of your building, the heating, cooling and lighting, the municipal services and taxes, all quietly add up every day and night, all year long. The vehicles and equipment in the yard, the tools and specialized technical gear, all represent significant investments of capital. People in the office who perform the maintenance, administration and management roles that keep the business operations working smoothly add regular compensation costs, rain or shine.
Or maybe it’s just you in the cab of your pickup truck, with your lead hand, a couple of skilled workers and a laborer or two, with all the tools in the box on the back. Either way, the fact remains that running a business costs money whether anybody is actually keeping track of it or not. And staying organized and on top of those details is critical to the ongoing viability of your business.
Jobsite Intelligence
The dollars are in the details…
In order to break down all these different costs and track them against the revenues that they help to produce, many contracting firms are turning to jobsite data management software.
With software automating the information collection, the challenge then becomes what to do with the data, records and reports that such software programs typically generate.
What is activity based costing and how does it work
One accounting and management method that can yield meaningful results is activity based costing, also referred to as ABC costing. This is a method of tracking the total costs associated with delivering a product or service. ABC includes an allocation of overhead costs to each step in the production process, in proportion to the amount of revenue or production generated by any one of these steps.
The primary advantage of the ABC system is that the relationship between specific cost amounts and specific activities are clearly identified. This transparency provides opportunities to identify and control overhead costs on an item by item basis. It also allows for accurate assessment of actual task and project costs versus “best guess”.
This translates directly into more accurate estimates and bids for future projects, with reference to actual costs and schedules driving the calculations for the successful completion of the work. The information obtained this way can be used to make decisions about the profitability of different types of projects and work processes. It can also drive changes to the way projects and processes are handled if the numbers point to a better way.
It’s As Simple As ABC
If it’s really that simple, why isn’t everybody doing it already?
In fact, while ABC is widely used across all kinds of different industries, there are certain issues that come into consideration when implementing a new ABC program from scratch.
For starters, the detailed math involved in some of the analysis can look intimidating to the amateur accountant. But don’t despair. For most contractors, a useful working model of ABC is going to be more simple than complex.
There is a cost of time and staff training involved in the analysis of current systems and in rolling out new data collection and reporting procedures.
Also, not all back-office overhead details relate equally to all field-based work projects and processes. It takes time, collaboration, and consultation with all stakeholders to fully implement and integrate an activity-based costing system. But the payoff comes in the eventual impact on the bottom line, and in the ongoing cost and time efficiencies that benefit employees, managers, and customers alike.
Why Does This Always Turn Out the Same Way?
Activity based costing will reveal details that define certain jobs. These details can include things like the cost of extra setup and removal time for a particularly complex activity. It can account for the actual cost of extra time spent in completing safety measures required by a certain type of working condition or environment. These are just some of the factors that can have a critical impact on profit and loss if they are not properly recognized and priced in.
The point is, the ABC system will show you how you’re making, or losing, money.
A challenge for any business is how to answer the tough questions. By breaking down the details and measuring the actual costs you make it easier to answer those questions.
- What can be done to improve or streamline how we organize our jobsite?
- Is there extra setup cost that wasn’t fully reflected in pricing estimates for bids and job quotes?
- Are there steps that can be taken in training, or investments made in equipment, that will reduce the cost on a permanent basis going forward?
These are questions that give business owners the opportunity to either increase efficiency or increase pricing to reflect actual costs. The secret to unlocking all this valuable business data is in the definition and use of cost codes. Cost codes and time tracking go hand in hand in the setup and operation of an ABC system.
If I Could Save Time in a Bottle
Time is never spent in a vacuum. When a company integrates information in an ABC system, with time tracking and strategic cost codes, employee labor time is always connected to all other meaningful project assets and activities, from equipment used to special instructions required. In modern digital management systems, this information can be sorted and reported in real time, on demand, by anyone connected with the job.
Armed with accurate historical information, project managers and technical workers can be more proactive in adapting their work processes to reflect past experience. And with real time job progress and cost monitoring, resources can be moved where they need to be based on actual numbers and known cost consequences.
This open access to actual costs of typical work activities and associated assets makes it possible to manage projects effectively by the numbers, rather than by guesswork and good intentions.
Let busybusy Do the Heavy Lifting
Activity based costing is one of the best ways to use historical experience and data to drive present and future efficiencies in production and profitability. At the heart of a good ABC setup is a user-friendly, fully automated time tracking application like busybusy, that produces the labor and equipment data required.
With everything that busybusy can do, from Jobsite Intelligence to Quickbooks payroll automation, you owe it to your bottom line to sign up today, or schedule a free demo and discover exactly what busybusy can do for you.